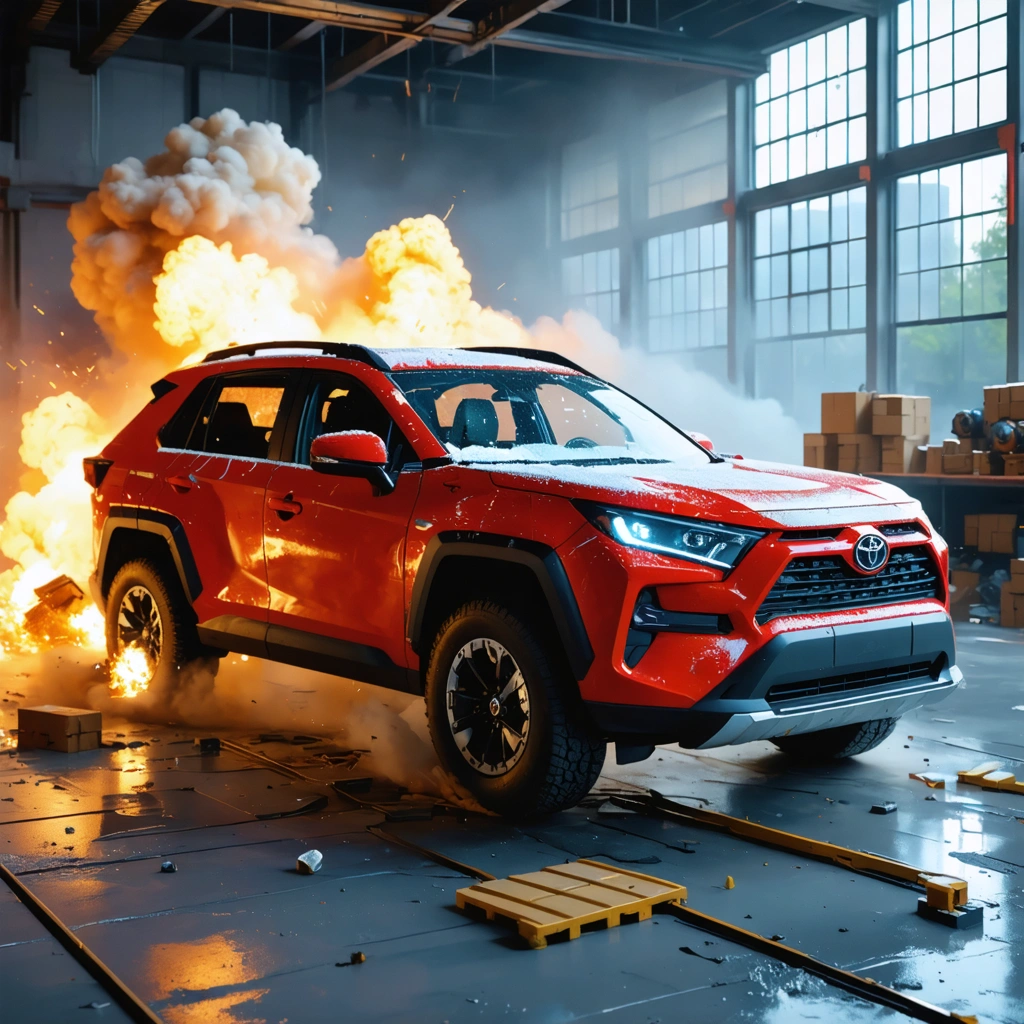
Overview of the Incident
The recent fatal explosion at one of Toyota’s key production facilities, which halted the manufacturing of the popular RAV4 model, has sent shockwaves across the global automotive industry. This unexpected incident, which the authorities are still investigating, has raised concerns over production safety, operational risks, and overall industrial resilience. Business stakeholders and supply chain partners are carefully monitoring the situation, as the repercussions of the shutdown could potentially extend far beyond the immediate disruption, affecting market dynamics, investor sentiments, and the company’s long-term strategic planning.
Immediate Impact on Production
Operational Disruptions
The explosion has resulted in a significant pause in RAV4 production. Key operational disruptions include:
- Shutdown of critical assembly lines
- Reallocation of safety and emergency resources
- Temporary suspension of deliveries to dealerships
- Potential cascading delays throughout the automotive supply chain
This list illustrates the multifaceted challenges that Toyota is currently facing. Each disrupted process not only affects immediate output but also contributes to a broader chain reaction impacting suppliers and downstream logistics efforts. The uncertainty regarding the duration of the halt has further complicated recovery planning.
Human and Economic Costs
In addition to operational challenges, the explosion has had severe human and economic tolls. The tragic loss of life has prompted a deeper review of safety protocols and a call for enhanced regulatory measures within the automotive manufacturing sector. Economically, the halt represents:
- Short-term revenue losses due to halted production
- Increased insurance claims and potential liability costs
- Reputation risks affecting investor confidence and consumer trust
In managing these impacts, Toyota’s leadership has faced a dual challenge: ensuring immediate support for affected personnel while also strategizing long-term recovery plans that encompass safety upgrades, process reengineering, and comprehensive stakeholder communications.
Risk Management and Safety Enhancement Measures
Reviewing and Overhauling Safety Protocols
The incident has accelerated the call for reviewing and overhauling existing safety protocols within operational facilities. Key initiatives include:
- Conducting exhaustive internal audits of all critical manufacturing processes
- Partnering with global safety consultants to establish industry best practices
- Implementing advanced monitoring and early-warning systems across production zones
- Enhancing employee training programs focused on emergency response and hazard identification
By adopting these measures, Toyota aims to not only address the current issue but also to prevent future occurrences and minimize potential risks across its diverse production network.
Strategic Recovery Planning
A critical component of Toyota’s response is its multi-layered recovery strategy designed to mitigate short-term disruptions while fortifying long-term operational resiliency. The recovery plan involves:
- Assessing Structural and Process Deficiencies: An in-depth investigation into facility operations and preemptive adjustments to mitigate risks.
- Collaborating with Stakeholders: Engaging with employees, suppliers, dealers, and regulators to establish coordinated recovery actions.
- Integration of Contingency Protocols: Developing robust contingency measures that address both immediate safety concerns and future production continuity.
- Communication Strategies: Maintaining transparent, real‐time updates to build trust among investors, customers, and the broader market.
These initiatives underscore Toyota’s commitment to managing the crisis proactively, ensuring that production lines are restored as quickly and safely as possible while prioritizing sustainable operational practices.
Long-Term Business Implications and Industry Outlook
Market Repercussions and Supply Chain Dynamics
The temporary shutdown has broader implications for the automotive market. Supply chain disruptions are likely to result in:
- Short-term fluctuations in vehicle availability and pricing
- Potential shifts in supplier negotiations and contractual agreements
- Longer-term strategic moves towards diversification and decentralization of manufacturing hubs
An industry table below summarizing core factors and probable outcomes has been prepared to illustrate these dynamics:
Factor | Short-Term Impact | Long-Term Strategy |
---|---|---|
Production Delays | Reduced output and order backlog | Establish contingency plans and bolster alternative supply channels |
Safety Protocols | Increased immediate regulatory oversight | Implement comprehensive risk management systems |
Market Trust | Potential decline in consumer confidence | Enhance transparency and strengthen stakeholder engagement |
Strategic Adjustments for Future Resilience
Looking ahead, Toyota and its industry counterparts are expected to re-strategize their operational models to mitigate future disruptions. Key strategic adjustments include:
- Investing in digital transformation to integrate advanced analytics with production management
- Strengthening interdepartmental communication to ensure rapid decision-making in crisis situations
- Exploring diversification across geographic and product lines to distribute risk
- Enhancing collaboration with regulatory bodies to set new industry standards for safety and efficiency
These adjustments not only address immediate operational concerns but also set a foundation for more resilient and adaptive business processes in a rapidly evolving global market.
Conclusions and Future Outlook
Impact on Toyota’s Strategic Vision
The fatal explosion that halted the production of the Toyota RAV4 has undoubtedly challenged the company’s strategic vision and operational resilience. As Toyota navigates through this crisis, the experience highlights several critical lessons:
- The importance of robust safety and risk management protocols
- The need for agile response mechanisms in preventing cascading operational impacts
- The significance of transparent stakeholder communication in fortifying market trust
While current investigations will determine the depth and cause of the incident, Toyota’s roadmap for recovery is expected to set industry benchmarks for crisis management and resilience planning.
Future Industry Opportunities
In grappling with the immediate fallout from the explosion, the automotive industry is likely to see significant shifts such as:
- Accelerated investment in next-generation manufacturing technologies
- Enhanced collaborations between industry leaders and regulatory authorities
- Improved integration of digital solutions and predictive maintenance strategies
- Development of a more distributed manufacturing model that reduces dependency on single plants
Ultimately, the lessons learned from this unfortunate incident will enhance safety protocols, operational efficiencies, and strategic planning not only for Toyota but for the entire automotive sector. The focus on resilience and proactive risk management will pave the way for a safer and more innovative industry future, transforming challenges into opportunities for robust growth and improved operational standards.